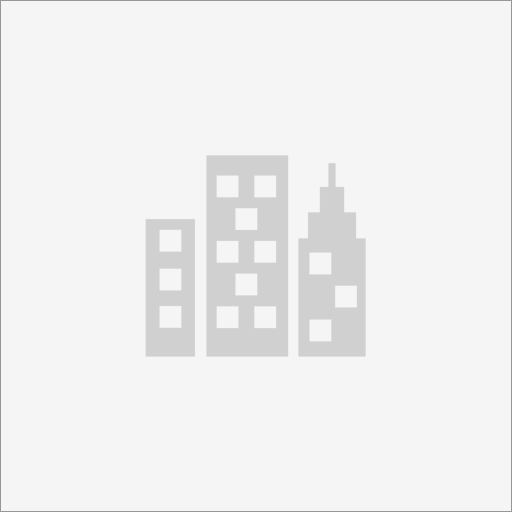
ACG World
Strategic and planning
- Define the long term strategy for CI in alignment with the business strategy
- Identify yearly Improvement areas and accordingly plan/prioritize projects for the plant
- Plan & Align resources, trainings and provide support as needed
Functional
Core
- Review and sign off detailed project plans for all identified CI projects in the plant including DMAIC activity plan for each project
- Analyze project data and conduct observation studies in every project
- Review action plans for project delivery (for every CI project at the plant)
- Monitor and communicate project status periodically to all stakeholders
- Preparation of 6 sigma (Black Belt/Green Belt/Yellow Belt) Training Calendar and ensure execution as per the timelines
- Facilitate implementation of Kaizen Mechanisms to drive small improvements across the plant
- Creation of Small Group Activity teams / Quality Circle Teams for Problem Solving.
- Conduct Value Stream Mapping/ Bottleneck and Cycle Time studies for Process Improvements
- Coordinate with Central CIC team to showcase the Improvement practices in the plant for replication across other plants
- Oversee daily project wise actionable/observation studies/trials and monitor the project participation of the stakeholders through various systemic methods
- Support Manufacturing/Production Project Leaders to conduct trials as per protocols
- Create, review and sign off of training module for various CI skill sets (TPM, Six Sigma, etc.)
Internal process
- Weekly Project Reviews with Plant Project team, Plant Head and Functional CIC Head
- Monthly Plant Steering committee reviews
- Escalate delays and non-compliances to expedite action
- Create, Review and periodically discuss the Projects Dashboard with Plant Heads
- Conduct GEMBA walks with Plant Head to regularly identify potential areas of improvements and review the status of improvements identified
- Conduct Kaizen Idea Workshops across the plant
People development
- Identify and Train people for Kaizen. Identify & develop project teams for analytics and sustenance of improvements
- Conduct Certification Exams
- Conduct Quarterly Kaizen Events for employees and build award mechanisms around it
- Conduct Yearly Six Sigma Project competitions
- Prepare plant teams for participation in Internal and External Events
A. Educational and Experience Requirements
Minimum Requirement
Desired
Level of Education
- BE/B-Tech
- MBA/M Tech (Operations/IE)
Experience
- 6 to 10 Years
Must Be
- Black Belt Certified
- Certified PMP, Data Analytics, Lean